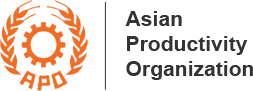
Select Page
Contributed by Mr. William Lee, Planning and Operations Management Group, Singapore Institute of Manufacturing Technology
The study mission was coorganized by the APO and Japan Productivity Center for Socio-Economic Development (JPC-SED) and attended by 18 delegates from India, Iran, Lao PDR, Malaysia, Mongolia, Pakistan, the Philippines, Singapore, Sri Lanka, Republic of China, Thailand, and Vietnam representing ministries and trade organizations, university faculties, and senior and middle managers in manufacturing firms. One project objective was learning about the lean production/manufacturing system through workshops and plant visits to Japan-based manufacturing companies. Lean production is considered the best way to improve company competitiveness and performance. It was evident from the country papers presented that many manufacturing firms have started to adopt lean production and tangible improvement has been seen. However, most of those firms have only adopted a small subset of the tools and concepts involved, and a clear roadmap for implementation as well as the management of this change process is lacking.
Lee (center) cochairing country paper presentations
Which lean initiatives should we start with?
The first key concern that surfaced during study mission deliberations was the search for an appropriate roadmap to guide the adoption of lean systems. Although lean concepts have been well documented over the past two decades, success stories of full-scale, companywide lean adoption are few. Most participants highlighted the difficulty in kick-starting lean improvement programs in their companies, particularly in deciding which initiatives to begin with. Detailed roadmaps will differ among companies due to differing work cultures, and most people are naturally resistant to change. Therefore it is best to start with a simple activity that causes minimal disruption to existing operations or processes. Once the people involved in the change process are comfortable with the change and note the tangible benefits derived, the entire change process will gain traction and the organization will be ready for more significant changes. It should be noted that all lean initiatives involve investments in the form of effort and initial disruption of ongoing operations. Thus, for a lean improvement program to be successful, quantifiable benefits need to be demonstrated clearly with the necessary timeline and resources provided. This will ensure that all staff buy into lean projects, which should be measured and managed like any other project in the company.
Listening to a presentation on productivity improvement activities at Fuji Heavy Industries Ltd.
President Yasuo Horiuchi, Horiuchi Engineering Institute, explaining a molding process
Plant observation at US Engineering Co., Ltd.
Sustaining changes and making them new habits
A second concern highlighted was the difficulty in ensuring the sustainability of lean improvement programs. Old habits die hard. Most lean initiatives start off as planned, but over time people tend to fall back into the old ways of doing things. Motivation for change is the key issue. How can we motivate the people involved to embrace the changes and make them their new habits? It must be recognized that changes cannot happen overnight and some form of catalyst is necessary to start the change process. Monetary rewards may work in the beginning but cannot sustain the change alone. A sense of ownership and recognition for making improvements are keys to sustainability. An organization should not manage too many change programs at the same time as the disruptions caused may be discouraging and counterproductive. Changes should be incremental and managed as a well-planned, continuous improvement process. Changes and their purpose must be communicated clearly to all involved. Improvement must be tracked, managed, and rewarded accordingly. Problems identified or discovered should be treated as opportunities for improvement rather than for assigning blame. With an open attitude toward problem solving, the organization will be more motivated to change for the better.
Can we improve indefinitely?
The third concern involved the end goal of all lean improvement programs. When productivity and efficiency improve through a lean program, the organization will be able to do more with fewer resources. The question is what happens if people are made redundant via the same process they helped to improve. Can improvement go on forever while maintaining the current workforce? The answer to these questions lies in the growth strategy of organizations. One obvious method to save costs is reducing the workforce. Hence, when an enterprise is able to achieve more with fewer resources after putting a lean improvement program in place, the next logical step is to remove the excess staff and achieve cost savings. However, this is a demotivating factor that will inhibit any future lean improvement initiative. An organization must have a business growth plan as it gains operational efficiency through lean production. Redeployment of the existing workforce is the way forward, giving employees a sense of achievement and and motivating them to contribute to future change programs.
A commitment to manufacturing excellence
Lean production is not a fad but a commitment to manufacturing excellence. It is not a one-off project but a long-term plan for continuous improvement. A culture based on open problem solving and a plan for growth are the keys for sustainable change and improvement.