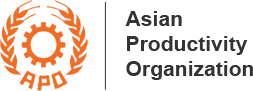
Select Page
Background
Over the years, lean manufacturing systems have become widely used by many companies as a fundamental methodology to increase productivity and reduce nonvalue-added waste. However, nowadays, when the principles of lean production are rooted in the spirit of many companies, some classic lean tools are beginning to lose advantage as room for improvement becomes smaller and improving is more difficult. However, in today’s global business environment, continuous improvement in productivity and quality remains the key factor to maintain profitability and competitiveness.
The introduction of Industry 4.0 with its principles of interconnection, information transparency, technical assistance, and decentralized decisions with cyber physical systems, the Internet, and future-oriented technologies could further enhance human–machine interactions that may lead to new dimensions of improvement. Nevertheless, executing Industry 4.0 could be cost intensive for most SMEs and there are also concerns over whether technology could be replacing human work itself.
Companies practicing lean could face the dilemma of whether Industry 4.0 is replacing lean systems or can be integrated with lean concepts. Lean approaches such as finding and eliminating muda (waste) in the form of idle or failed machines or nonvalue-added activities could be improved by integrating Industry 4.0 principles. Applications of advanced data acquisition, sensors, and the Internet of things (IoT) and Internet of People make advanced analytics and real-time data access possible, which offers obvious advantages in finding and eliminating waste. Therefore integrating lean management systems with Industry 4.0 concepts could be referred to as “digitalized lean” to take operational excellence to entirely new horizons.
Based on research by Shah and Ward, lean manufacturing is divided into the following 10 key factors:
1. Supplier feedback
2. Just-in-time (JIT) delivery by suppliers
3. Supplier development
4. Customer involvement
5. Pull production
6. Continuous flow
7. Setup time reduction
8. Total productive/preventive maintenance
9. Statistical process control
10. Employee involvement
The 10 key factors could be further subdivided into four groups consisting of supplier, process, customer, and control and human factors for further evaluation of the possibilities of the implementation of lean through Industry 4.0.
Supplier factors
The robustness of information exchanges among customers, manufacturers or process owners, and suppliers determines the extent of pull production and JIT effectiveness. Industry 4.0 enhances those exchanges with radio frequency identification (RFID) signals that wirelessly link to cloud computing and customer feedback through apps or social media that boost information sharing. With a combination of RFID tagging, global positioning system (GPS) tracking, and synchronization of data, on-time delivery performance can be enhanced and customer complaints or product defects addressed instantly (Figure 1).
Figure 1. Combining RFID, GPS, and cloud-based feedback to improve supplier factors in integrated lean systems.
The use of technology networks and resource-sharing platforms enables better knowledge sharing from customers to suppliers, which could overcome the problems of bureaucracy and inadequate communications among the parties involved. At the same time, sharing and synchronizing data among suppliers could enhance the effectiveness of supplier development with benchmarking against the best practices.
Customer factors
Getting customers involved from the product development stage has proven critical for businesses to survive. Customer involvement can be enabled with the use of online platforms such as the Lego ideas page, which allows companies to develop popular products based on customer feedback (Figure 2).
Figure 2. Sample Lego Idea Page and a product developed through customer feedback.
With the availability of real-time data access, customers can track and trace the progress of production processes and be updated on delivery times. The user experience could be fed back in a loop of information starting from the design development to final product use. This would provide a complete picture for continuous improvement over the entire product life cycle. The involvement and participation of customers throughout that cycle could also contribute to their greater satisfaction and loyalty.
Process factors
Pull production can be enhanced with RFID tagging that enables the status monitoring of workpieces (finished goods or work-in-progress products) and real-time tracking of quantities and locations as well as communication with machines. With the use of such ICT, e-kanban systems can identify and trace any missing or vacant slots for replacement orders while sharing inventory data wirelessly in real time. Changes in schedules can also be continuously monitored and kanban parameters updated instantly. As a result, the pull system of production would be enhanced with automatic material replenishment monitoring, schedule tracking, and kanban updating with through Industry 4.0 facilities.
The establishment of machine–workpiece communication and self-optimization of equipment will improve the ability to achieve high-level customization and small-batch production as each piece can be identified with a unique RFID tag that communicates directly with machines. That will result in reduced machinery setup or changeover times.
Control and human factors
Industry 4.0 enables total productive maintenance operations with automatic notifications from machines when errors or breakdowns are detected. At the same time, error messages also trigger the e-kanban to reschedule production plans and notify interested parties. Maintenance personnel can prepare for repairs based on error coding resulting from previous data analysis and proposed countermeasures from primary cloud computing analysis (Figure 3).
Figure 3. Control and human factors in an integrated lean/Industry 4.0 system.
While RFID enables automatic sensing of processes for variations linked to machine stoppage data to prevent further rejections, the industrial IoT assists in integrating data from different machines for big data analytics for the acquisition of advanced business intelligence to ensure defect-free production (Figure 4).
Figure 4. Linking RFID technologies and the industrial IoT gathers intelligence for defect-free production systems.
Employee involvement
With the application of Industry 4.0, production workers are able to provide immediate feedback and comments in real time via smart phones or tablets. The data can be sent for company-wide collection linked to the use of big data. The evaluation of workers in term of speed, accuracy, performance, and motivation can also be simplified and visualized through specialized interfaces to enhance worker support systems.
How SMEs can integrate lean and Industry 4.0
Through integrating robust Industry 4.0 ICT applications, organizations implementing lean systems will reap the combined benefits of real-time information and waste elimination to enhance the performance of the key supplier, customer, process, and control and human factors. This gives organizations, including SMEs, the potential to expand into new horizons with ease. The integration of Industry 4.0 with current lean management systems is not limited to the IT, quality assurance, and production departments but can benefit the entire organization including the supply chain, customers, and other parties involved.
As cheaper, faster, more flexible robots, sensors, technical solutions, advanced analysis algorithms, and connectivity options become commonly available, the integration of lean and Industry 4.0 could occur sooner than most SMEs expect. Nevertheless, it will involve intensive investment and potentially result in comprehensive changes in organizations. Most research on Industry 4.0 remains in the theoretical stage or on an initial trial basis, and possible solutions have yet to reach the stage of practical, marketable maturity. Organizations preparing to introduce Industry 4.0 could start with small-scale research and continuous improvement in a controllable, affordable manner. Top management should take ownership and participate directly in efforts to transform to Industry 4.0 integrated with lean systems to ensure success.
Alex Yap is the expert for the APO e-learning course on Integrating Lean Manufacturing Systems and Industry 4.0 Concepts. Course description is available here.
Alex Yap has more than 15 years of manufacturing experience as a quality assurance manager. He is a registered consultant with the Malaysia Productivity Corporation, a business excellence assessor, and productivity specialist in the areas of process improvement and performance excellence. Alex also served as a technical expert for various APO Green Productivity, lean, and material flow cost accounting courses.