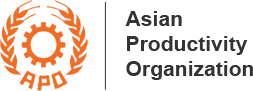
Select Page
Introduction
The common notion about smart manufacturing is that it involves the application of digital technologies, such as the Internet of Things, wireless networking, artificial intelligence (AI), big data analytics, augmented reality, cloud computing, etc. While this may not be factually incorrect, smart manufacturing is not just about implementing digital technologies. The technologies are simply enablers. This article explains the smart manufacturing concept through definitions commonly used in industry.
Definition of smart manufacturing
Smart manufacturing improves performance. The business driver of smart manufacturing is the need for improved productivity, quality, customer responsiveness, supplier relationships, and thereby overall improvement in a firm’s competitive advantage. There are many definitions of smart manufacturing in the literature. MESA International, a well-known, not-for-profit organization of manufacturers, producers, industry leaders, and solution providers which is involved in knowledge diffusion, best practice training, and advocacy, uses the following definition:
“Smart manufacturing is the intelligent, real-time orchestration and synchronization of business, physical and digital processes within factories and across the entire value chain. Resources and processes are automated, integrated, monitored and continuously evaluated based on all available information as close to real-time as possible.”
The key phrases in this definition are “intelligent, real-time orchestration,” “synchronization of physical and digital processes,” and “across the entire value chain.” Each of these key phrases is examined below.
What is intelligence?
The first attribute of a smart manufacturing process in the definition above is intelligence embodied in a system/controller or more basically in a computer program. Intelligence can be defined in different ways, but in this context it is the ability of a system, controller, or computer program to apply knowledge to solve a problem, even in the presence of uncertainty and/or incomplete information. If intelligence is the ability to apply knowledge, then what is knowledge? Knowledge can be defined as a new understanding derived from the facts, data, and information available.
Applying these concepts to a manufacturing environment, machines are deployed to produce products. As shown in Figure 1, if appropriate sensors can be interfaced with machines and/or processes we can start collecting data on the key process variables of machine operations or processes during every cycle.
Figure 1. Embodiment of intelligence in a controller/system of a smart manufacturing process.
This data stream can then be used to “understand” the status of the machine/process, such as whether it is operating optimally according to the manufacturer’s guidelines and/or according to the designed process capability. This understanding becomes new “knowledge.” The knowledge can then be applied to maintain the process at or near optimality. Therefore, in the context of smart manufacturing, a system, controller, or computer program that can collect raw data from machines, transform raw data into meta-data or knowledge to achieve an understanding of the status of the machine and/or process, and apply the discovered knowledge to suggest and/or implement appropriate course corrections to achieve optimality in performance represents the embodiment of intelligence.
The above is still not a complete definition of intelligence as it does not cover all conditions involved. The second part of the definition of intelligence above states “even in the presence of uncertainty and/or incomplete information.” It is important not to assume that the understanding and application of knowledge can be achieved only in the presence of certainty and complete information. That would be impractical in a manufacturing setting, as 100% of the information required to make decisions can never be captured. There will always be some gaps in knowledge and/or the presence of vague, ambiguous data. Those uncertainties can be characterized using statistical, probabilistic, or AI techniques.
Therefore, intelligence in the context of smart manufacturing can be defined as: “A system, controller, or computer program that can continuously collect raw data from machines, transform the raw data into meta-data or knowledge to achieve an understanding of the status of the machine and/or process in spite of inaccuracies and insufficiencies in the data, and apply the discovered knowledge to suggest and/or implement course corrections to achieve the desired optimality in performance (such as improved productivity) represents an embodiment of intelligence in the context of smart manufacturing.”
Real-time orchestration
While the word “intelligence” is often used in industry, the phrase “real-time orchestration” is relatively less common. “Orchestration” is well understood in music, but what does it have to do with smart manufacturing? Orchestration also refers to coordinating the elements of a process to achieve the desired overall effect (such as improved productivity or efficiency). It thus refers to the coordination of multiple elements of a manufacturing process to achieve the goals of a production facility. The definition of smart manufacturing states that orchestration must be in real time or as close to real time as possible. That is, any embodiment of orchestration in a controller/system or computer program in the context of smart manufacturing must exhibit real-time capability.
What are the processes involved in orchestration? They include but are not limited to coordination among multiple related processes and reconciliation among multiple conflicting processes.
Intelligence is a necessary condition for real-time orchestration, but it is not sufficient alone. Beyond intelligence, collaboration and coordination among processes, as derived from corporate policies, are necessary. Figure 2 shows an example of real-time orchestration in industry for achieving asset performance management. In this case, the real-time orchestration is embodied in a product called Enterprise Gateway, a trade name owned by 5G Automatika Ltd., Canada. The objective of the system is to achieve optimal performance of critical assets and to reduce or eliminate unplanned downtimes by appropriate predictive, preventive, or prescriptive maintenance interventions.
Figure 2. Example of real-time orchestration of predictive, preventive, and prescriptive maintenance to improve availability, which translates into improved productivity.
Source: Produced by the author; copyright 2019–20 held by 5G Automatika Ltd., Canada.
As shown in the figure, the product reconciles real-time and historical asset conditions on one hand, and asset life cycle/maintenance information (such as failure histories, maintenance intervention costs, maintenance resource availability, asset operational conditions, manufacturer’s guidelines, ambient conditions, etc.) on the other, for all of the critical assets in the plant. This reconciliation is aimed at generating timely, proactive (prescriptive, predictive, or preventive) work orders for the assets if there is a possibility of an imminent failure or downtime. The overall objective is to reduce unplanned downtime and to improve plant availability. When availability improves, overall equipment effectiveness, a commonly used metric for manufacturing performance, improves. The orchestration also shows the coordination/collaboration enabled between multiple stakeholders, like maintenance supervisors, senior managers, plant supervisors, and maintenance personnel.
Synchronization of physical and digital processes
After defining intelligence and real-time orchestration, the meaning of “synchronization of physical and digital processes” should be explained. Most readers know the meaning of “physical processes” in the context of manufacturing. Every physical process can be represented by a flow diagram with inputs, process variables, and outputs. Different states of the physical process can be identified for different sets of input conditions.
Physical processes are present in every manufacturing operation. In a CNC turning machine, for instance, the depth of cut, feed, speed, etc. are all process variables. The process cycle of the turning operation may be divided into the three phases of loading, turning, and unloading with an overall cycle time attributed to the entire process.
A “digital process” is simply a representation of the physical process. The example turning process can be presented visually in a digital dashboard as a sequence of the three phases mentioned above. Sensors in the machine and the environment identify the loading and unloading cycles. Sensors in the machine measure the cutting time. The values of the process variables during cutting can also be measured using sensors. This raw data stream generated by sensors can be visualized in the same sequence of phases in an interactive dashboard on a tablet. In other words, as each phase is performed, the corresponding section of the digital dashboard representing that phase can be updated in real time. By visualizing the digital process flow as an equivalent of the actual physical process flow in real time, the digital and physical processes are synchronized. The synchronization of material and information flows is a fundamental aspect of smart manufacturing.
Beyond synchronization, the digital process can optimize the physical process. In other words, the intelligence derived from the digital process can be used to identify the root cause of process deviations from the optimal point. This can result in refinement of specific inputs or state variables in the physical process.
Integration of the entire value chain
Smart manufacturing is about integration, connectedness, and collaboration. Not only are machines and humans connected in a smart manufacturing process, the ecosystem of suppliers, original equipment manufacturers (OEMs), and customers is also interconnected. Such connectivity allows for the real-time monitoring of operations so that downtimes, delays, quality issues, etc., are immediately known to downstream stakeholders in the logistics chain. OEMs can therefore respond/adapt appropriately to the changes.
Figure 3 illustrates the integration of a supplier’s quality process with an OEM. Inspection data at the supplier’s site are acquired objectively without the need for an operator’s data entry. This eliminates errors and omissions normally attributed to human fallibility and stress. In other words, in this example, the operator merely makes the required dimensional measurement of the part using a vernier or a dial gauge. As the measurement is made, the dimensional data corresponding to that measurement are acquired automatically using a digital attachment to the vernier or dial gauge. The digital data are transmitted wirelessly to a cloud server, to which both the OEM and the supplier have simultaneous access. This digital process of inspection synchronized with the actual physical process of inspection performed by the operator allows for the elimination of a quality inspector at the OEM. This is because the batch quality is already known to both the OEM and supplier before dispatch. Therefore, if the quality is not as specified, improvements are made prior to shipping.
Figure 3. Example of ecosystem integration for achieving standardization of quality between a supplier and an OEM. QA, quality assurance.
Source: Produced by the author; copyright 2019–20 held by Fifth Generation Technologies India (P) Ltd.
Conclusion
The descriptions of specific terms used in smart manufacturing provide readers with a clearer understanding of this concept. The descriptions show that smart manufacturing involves intelligence, real-time orchestration, synchronization and optimization of physical and digital processes, and collaboration/integration of the entire ecosystem. The combination of all of the above, enabled by smart technologies such as the Internet, WiFi, bluetooth, AI, augmented reality, simulation, big data, etc., allows continuous optimization of manufacturing performance (such as maximizing productivity and quality while minimizing costs), improvement in the return on assets, and thus a better competitive advantage and increased market share.
Dr. Ananth Seshan is the expert for the APO e-learning courses on Smart Manufacturing.
Click course titles below for course description.
Smart Manufacturing: Basic
Smart Manufacturing: Advanced
Dr. Ananth Seshan is Chairman of the 5G Group., a multi-national digitalization solutions provider in the manufacturing industry. He is a member of the International Board of MESA International, a not for profit organization headquartered in the US focussing on best practices for implementing Industry