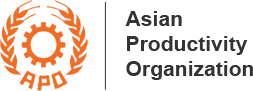
Select Page
PDCA stands for “plan, do, check, and act.” The PDCA cycle is a checklist of the four stages one must go through to get from “problem faced” to “problem solved.” The four stages are carried out in the cycle illustrated below. The concept of the PDCA cycle was originally developed by Walter Shewhart, the pioneering statistician who developed statistical process control in Bell Laboratories in the USA during the 1930s. It is often referred to as “the Shewhart cycle0”. It was promoted very effectively from the 1950s on by the famous quality management authority, W. Edwards Deming and is consequently known by many as the Deming cycle or Deming wheel. The following is a description of PDCA:
Plan: Determine the root cause of the problem and then plan a change or a test aimed at improvement.
Do: Carry out the change or the test, preferably on a pilot or small scale.
Check: Check to see if the desired result was achieved, what or if anything went wrong, and what was learned.
Act: Adopt the change if the desired result was achieved. If the result was not as desired, repeat the cycle using knowledge obtained from the previous cycle.
Although this is a continuous cycle, one needs to start somewhere. As a problem-solving process one would normally start at the check stage to identify what the requirements are and reality is. The gap between reality and requirements determines whether it is necessary to act. To use this as a problem-solving technique, a process must already be in place which can then be modified.