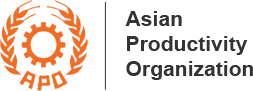
Select Page
An APO demonstration project in India created the new approach “Green Lean (GLEAN)” to integrate lean manufacturing and material flow cost accounting.
Gemba visit of APO expert Hiroshi Tachikawa at Reva Industries, Faridabad.
On his first visit as the APO-assigned expert for a demonstration project in India, Hiroshi Tachikawa, managing director of Propharm Ltd., asked the management participants of all five companies one simple question: “How well do you understand your company?” Unsurprisingly, everyone answered “100%.”
Commented Tachikawa, “This was typical of staff involved in a demo project. Of course, they answered 100%. However, as is often the case, it soon turned out that 30–40% of the necessary information was actually not available. That always surprises managers and motivates them to start the project.”
The project Tachikawa was working on with the National Productivity Council of India (NPC) involved material flow cost accounting (MFCA)-linked lean manufacturing for SMEs, leveraging the synergy of productivity enhancement methodologies to contribute to the “zero-defect, zero-effect” outcome.
MFCA is a steppingstone for productivity, quality, and waste minimization programs in manufacturing plants. It was first introduced in India in 2012, resulting in improvements in the overall utilization of material, resources, and energy as well as significant monetary savings and higher overall productivity in the companies involved in the initial APO demonstration project.
Lean manufacturing, on the other hand, is a systematic approach recognized as a solution for optimizing production streams and removing unnecessary waste. Over the past 10 years, the NPC, with its vast technical expertise, has successfully implemented a Lean Manufacturing Competitiveness Scheme in SMEs across the country.
Tachikawa and the NPC team decided to formulate a new approach to integrate those two powerful tools to gain maximum benefit in terms of productivity improvement coupled with environmental sustainability. They called this integrated approach “Green Lean (GLEAN).”
In a new APO demonstration company project, the GLEAN concept was adapted for implementation in five selected Indian MSMEs in the manufacturing sector (automotive, engineering, electrical). The participating companies were Modvak Engineering India Pvt. Ltd., United Cores Pvt. Ltd., Reva Industries Ltd., Sanatan Autoplast Pvt. Ltd., and Matrix Tools India. The project commenced in November 2016 and continued for 12–15 months including the follow-up dissemination activities.
Building on the past, not starting from scratch
As an expert in sustainable resource management, Tachikawa was confident that this demonstration project would be successful in linking productivity, environmental concerns, and financial performance. However, one big obstacle was changing mindsets. “That was because production staff focused only on outputs, while the finance teams concentrated only on budgets. Based on their roles and responsibilities, they do their best for each department or function, but this does not necessarily lead to the best situation from the perspective of GLEAN,” he explained.
Tachikawa, who has been involved in a number of environmental consulting projects, admitted that sometimes it was very difficult to convince all participants to share the same understanding that productivity is linked to greater financial benefit. It often took a lot of training to help them understand the general concept of GLEAN and its applications in their operations.
“We had multiple meetings and training sessions as well as some communication sessions to help them understand the GLEAN concept, which was key for the successful implementation of this project. All the demo companies were very cooperative as they understood this would be beneficial to them in many ways. I repeatedly emphasized that the start was not from scratch but from their past efforts. Existing kaizen/improvement activities, lean efforts, and management systems in place really helped employees to get GLEAN activities going smoothly.”
Tachikawa pointed out that the data-collection phases were also a big challenge. He and the NPC team dealt with that by giving technical advice on the possible uses of existing data and onsite support for collection activities.
Almost all of the initial objectives the project set out to achieve were met, in Tachikawa’s assessment, including improvements in the companies’ productivity, quality, environmental impact, energy efficiency, and safety.
Economic gains and environmental sustainability
Kick-off visit of APO expert Tachikawa along with the NPC India team at Modavk Engineering, Bahadurgarh.
One of the participating companies, Sanatan Autoplast, a manufacturer of plastic injection molding components for the automotive industry, was eager to join the demonstration project since it was facing several challenges including the lack of a systematic approach to resolve problems such as unidentified waste and poor inventory control.
After completion of the project, Sanatan Autoplast reported that with GLEAN methodology the company had overcome its main shortcomings, improving its productivity by 8–10% and reducing its rejection rate by half. It was able to achieve this mainly through real-time digital monitoring of production data as well as recording and analyzing rejected parts, performing preventive maintenance, and utilizing energy more efficiently. “The implementation of GLEAN resulted in savings amounting to USD35,935,” reported Sanatan Autoplast CEO Anik Kukreja.
United Cores, a leading local producer of aluminum diecast components and electrical stamping, realized that it was experiencing material losses in both those production areas prior to the demonstration project. “There was a lot of wasted iron during electrical stamping, and with the area lost from the original iron sheets, the yield ratio was low. Using GLEAN to overcome this, we decided on tool redesign to minimize the scrap generated and reduce manual operations,” said United Cores CEO Alok Goel.
“The manpower cost for diecast components was too high because additional staff had been deployed to one specific quantity center. We decided to undertake kaizen activities in the inhouse design functions and develop a tool to minimize operations while decreasing manpower deployment costs,” Goel continued. He reported that through GLEAN implementation, company savings had reached around USD43,045 annually.
He also believed that the project had made the company more data driven and teams more focused since, “Inputs and wastage are regularly discussed. Through this program, our team is more sensitively focused on all process inputs and waste.”
Meanwhile, Anoop Jain, Director of Matrix Tools, cited statistics to show how participation in the demonstration project had resulted in improvements in productivity (by 6%), longer tool life (by 4%), reduction of rejected parts (from 3.5% to 0.5%), and better environmental performance (negative products reduced by 2.5–3%). All those results led to less scrap generation and damage to the environment. “With the implementation of MFCA, lean manufacturing, and GLEAN actions, we have gained approximately USD45,900 in the first year,” according to accounting records.
Apart from those improvements, Matrix Tools was also seeing a change in employee mindsets as they were now more aware of waste and material costs. In the long term, Jain planned for the good practices and lessons from the project to be implemented in other areas too. “We will conduct improvement and cost reduction activities and introduce these measures in other processes. This will help Matrix Tools make more effective use of resources, raise productivity, and improve quality.” In addition, Jain described plans to link those activities with reducing environmental impacts by including MFCA, lean techniques, and GLEAN-related activities in the product design phase.
The other two companies in the demo project also reported monetary savings after applying GLEAN methodologies. For Modvak Engineering India, the annual savings was USD140,325, while for Reva Industries it was about USD21,050.
Reaping future benefits
The introduction of GLEAN in the five demonstration companies clearly showed benefits in terms of economic gains and environmental sustainability, declared the NPC’s Aman Gulati. “The application of GLEAN in the model SMEs resulted in greater material, resource, and energy savings with improvement in overall productivity. Moreover, GLEAN can be applied to the supply chain where material waste in individual organizations can occasionally be traced to a supplier source.”
Gulati also noted that, “The insights GLEAN provided have resulted in innovative suggestions for improving the manufacturing process. In addition, this project confirmed the effectiveness of integrating MFCA and LEAN.” He added that GLEAN implementation as a continuous improvement cycle had moved production processes closer to optimization, from increasing the economic effectiveness of production, to positively affecting the environment through energy savings, to creating a safer workplace.
When asked what the next step would be for the demonstration companies, Tachikawa identified a number of environment-related opportunities that could also yield cost reductions. He gave examples of waste elimination, greater efforts to analyze profit-and-loss statements, resource efficiency, and carbon reductions to emphasize his point.
Workshop on GLEAN and booklet launch event organized by the NPC on 15 February 2019.
Gulati agreed with Tachikawa’s suggestions, adding that, “GLEAN as an innovative, integrated technique helped the companies identify and then prioritize windows for improvement. It also served as a strong motivating factor since it showed the potential for tangible benefits in productivity, profitability, and environmental performance.”
The APO’s Green Productivity (GP) Program is based on broad strategies for enhancing productivity while simultaneously improving the environment. As confirmed in this demonstration company project, the philosophy of the integrated GLEAN approach as put into practice under the umbrella of GP can enhance the overall quality of life, socioeconomic development efforts, and enterprise prosperity.
Photos: NPC
0 Comments