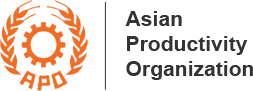
Select Page
How MFCA paved the way for higher productivity in two APO demo companies in Bangladesh.
NPO Director S.M. Ashrafuzzaman (center) exchanging a memorandum of understanding between representatives of SR Asia Bangladesh (2nd L) and Blue Ocean Footwear Ltd. (2nd R).
Leather and leather goods is Bangladesh’s second-largest export sector. While that’s great for the economy, distressingly the industry is linked to serious effects on the environment and leather sustainability. Realizing the downside, the government looked into adopting sustainable, environment-friendly green industrialization measures.
With that in mind, the National Productivity Organisation (NPO) of Bangladesh, in collaboration with Social Responsibility Asia (SR Asia), undertook an APO demonstration (demo) project to encourage the leather and footwear sectors, as well as others in Bangladesh, to use material flow cost accounting (MFCA)-based productivity improvement initiatives to benefit enterprises, workers, and all stakeholders.
MFCA is a powerful management tool that has assisted enterprises worldwide to raise productivity and capacity in resource management. It helps businesses to improve efficiency in utilizing materials and energy and contributes to reductions in nonproducts, waste, and emissions.
MFCA is used in tandem with Green Productivity (GP), a solution introduced by the APO as a practical way to manage sustainable development. It simultaneously addresses both economic development and environmental protection in the industry, agriculture, and service sectors.
The APO demo project in Bangladesh was carried out in two companies: Blue Ocean Footwear Limited, a 10-year-old manufacturer with more than 4,000 employees; and Kushum Kali Footwear Limited, with a workforce of 200.
“The two companies selected both specialize in shoemaking, and in order to gauge MFCA’s impact, we selected one established player and one mid-range company. We formulated a data sheet so that each could equip employees with MFCA knowledge and expertise needed at the factory,” explained Nazrul Islam of the NPO.
Nazrul said that the aim was to ensure that both shoemakers had achieved productivity improvement and spread the productivity mindset at the end of the project.
“We also provided productivity training. MFCA was extremely beneficial because it pinpoints where waste occurs and can be reduced. Less waste obviously has positive environmental effects in addition to decreasing energy consumption. That’s why this program will impact Bangladesh positively,” he added.
The duration of the demo project was 12 months, including the dissemination period, starting in January 2018. To ensure that implementation proceeded without major hiccups in these two companies, the NPO team approached Associate Professor Dr. Wichai Chattinnawat of Chiang Mai University’s Department of Industrial Engineering to guide it.
“When the NPO of Bangladesh approached the APO about starting a project to undertake GP transformation based on the resource efficiency concept, we were determined to set the guidelines for overall environmental and productivity improvement,” said Dr. Wichai.
The APO team kicked off with a diagnostic survey of the demo companies to get an overview of their business and production data. This was followed by a four-day training workshop on capacity building before focusing on the implementation aspects of the project.
Based on their initial legwork and visits to the companies, the APO team discovered unnecessary waste in the leather cutting and trimming processes, largely due to knife quality, cutting pattern variations, machine quality, and workplace management. During the assembly process, significant amounts of glue were also wasted due to poor management of the tools used.
Dr. Wichai said that it was a tough task from the start, not just because of the inherent challenges in the leather and footwear industry, but also because the demonstrations companies are SMEs, and their organizational and operational management as well as their shopfloors did not meet ISO standards. At the Kushum Kali factory, standardized work instructions and an effective productivity monitoring system were also lacking.
“It wasn’t just the staff and operators. Leaders and managers were also unfamiliar with, for example, productivity, the kaizen concept, or even the ISO,” pointed out Dr. Wichai. “Thus, we had to not only change their mindsets but also provide training and hands-on practical workshops. Luckily, MFCA is a very straightforward diagnostic tool to help identify the efficiency of resource use and waste generated.”
He went on to stress that, “It looks at the flows of materials from every connected process throughout the production plant and system. The good thing is that we can develop a methodology for applying the MFCA tool from the ground level if everything is not well organized. We actually spent a lot of time creating many building blocks such as productivity reports, check sheets, work instructions, and even process redesign,” Dr. Wichai explained.
The APO expert team started the ball rolling by identifying the causes of inefficiencies in the companies’ production processes. Once that was done, the teams in the participating companies received training on the 7 wastes, productivity improvement, line balancing, productivity and quality monitoring with check sheets, and real-time production control.
Assignments and workshops were combined and used to identify improvement opportunities based on the two demo companies’ actual processes. While both gave their full attention and cooperation to the MFCA project, the APO expert still needed to overcome other challenges.
“There were a couple of challenges that we faced with both companies. The data provided did not conform to the data needed to apply MFCA. For example, the actual material consumption was not recorded in total and it was very difficult to proceed with the development of an MFCA plan without this basic information. In addition, records on the processing time spent on each product and energy consumption were also incomplete,” he said.
Dr. Wichai Chattinnawat (2nd R) on a factory visit to Blue Ocean Factory Limited to collect data with NPO Officers Ripon Saha (3rd R) and Syed Zayed-ul-Islam (R).
The APO team overcame the problems by developing and designing all check sheets, forms, and production records to be used to collect necessary data, which meant that the demo companies could start to monitor their own process efficiency.
Another challenge involved MFCA analysis and interpretation, which require calculation and computer skills. Unfortunately, those skills were lacking. Dr. Wichai was able to develop an Excel-based MFCA calculation technique and show company managers how to connect all recorded data with MFCA analysis, which led to the desired results.
Another component the APO expert stressed was team collaboration: “It is the key success factor clearly stated in ISO14051: MFCA standard. For instance, at the Blue Ocean Company, the accounting manager came onboard to validate and verify all costing and accounting. This kind of mutual collaboration was essential to achieve our project goal.”
Considering the time constraints, participants’ initial lack of knowledge, and the fact the project was based on a specific product line for demonstration, the APO team was pleased with the outcome.
“It’s good to see both companies implementing our recommendations but they must also continuously apply the methodology learned from this project to every product. They need to think about using it from the product planning stage. If it is fully and consistently implemented, the GP goals can be achieved,” commented Dr. Wichai.
At the end of the demo project, new forms of production and quality control were devised and utilized so that waste generated from rework was significantly reduced and output increased. Kushum Kali Footwear successfully decreased the amount of leather and synthetics wasted in production. It also reduced glue consumption. The overall implementation of MCFA is projected to lead to annual savings of at least BDT1.4 million (USD16,500) for Kushum Kali Footwear.
Blue Ocean Footwear is forecast to save at least BDT5 million (USD58,900) per year in material costs alone. Total material consumption can be reduced by 30,000 square foot of high-value leather annually.
After the MFCA demo project obtained tangible results, Dr. Wichai hopes that the NPO can extend the methodology to all leather and shoe manufacturers in Bangladesh. “Both companies can now reduce synthetic and genuine leather consumption, which is expensive. This project also showed how to lower glue losses and energy consumption, which was clearly reflected in the real cost reductions and annual savings of Kushum Kali Footwear. It has also led to greater process management efficiency, fewer defects, and less material consumption.”
The APO expert believes that the success of the project will create opportunities for the NPO to convince more companies to undertake GP efforts at the national level. The NPO’s Nazrul agrees: “The outcomes of the project are very positive. Both companies reduced their costs significantly by reducing waste. This shows that MFCA can definitely be implemented in shoe factories.”
He added that the most valuable outcome of the project was developing a productivity mindset. “MFCA was a very new tool to Bangladesh, yet the companies managed to adapt it smoothly. I’m certain that other APO member countries will be inspired by this project. We believe that if the mindset is positive, then any productivity tool or technique can be applied successfully.”
Nazrul also reported that the NPO had arranged a seminar at the completion of the demo project to share the success stories of the two companies. “There were more than 100 representatives present. Now other enterprises can learn from these two demo companies how to implement MFCA. That will help our leather sector as well as the SME sector in Bangladesh.”
Photos: NPO of Bangladesh
Click here for the documentary video on this demonstration project produced by the NPO of Bangladesh.
0 Comments