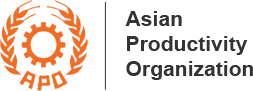
Select Page
A demonstration project showed how smart solutions in MSMEs yield multiple benefits while cutting costs.
Introduction
The Indian automotive industry, with deep linkages to multiple subsectors of the overall economy, has powerful multiplier effects. Its prominent place in the national economy made it an obvious candidate for a demonstration company project under the Asian Productivity Organization’s (APO’s) Smart Manufacturing Transformation Program.
When the MSME Vibgyor Automotive Private Ltd. (VAPL), a manufacturer of steering and brake components with annual turnover of USD8 million, was selected as a demonstration company by the APO and National Productivity Council (NPC), Director of Business Development Harish knew that the company had an opportunity to put the Internet of Things (IoT) and Industry 4.0 technologies at the heart of company operations. It was clear that the potential value generated by the project could make VAPL a role model in India’s fast-changing industrial scene.
Interaction with the plant supervisor during the diagnostic survey conducted at the demonstration company Vibgyor Automotive Private Ltd.
In the initial evaluation stage of the project, issues of concern were identified by the APO-assigned technical expert Dr. Ananth Seshan and NPC project coordinator S.M. Samdani. They cited VAPL’s material losses, quality aspects, production monitoring, ensuring material availability, and decision-making processes as general areas for improvement. Specific weaknesses included incomplete tracking or delayed entry of records on rework and rejects; omission of measurements; subjective quality checks; manual entry of measurement, production monitoring, and other data; delayed access to information; lack of or delayed information on order status from raw material suppliers; inconsistent follow-up with suppliers; and abnormalities noted only at the end of the month.
Director Harish’s initial task was ensuring that VAPL employees were prepared to accept and learn how to apply technology-based smart solutions to overcome the weaknesses. “From the outset, we laid out areas that we needed help with and were very committed to the project,” he explained. In cooperation with the expert and NPC coordinator, VAPL held a workshop involving workers and management to introduce the project, show the big picture, and solicit the necessary cooperation at the shopfloor level.
The demonstration project started in December 2017 and was scheduled for completion within 12 months. According to the action plan, the first eight to 10 months were allocated for execution and the remaining two for dissemination activities.
Overcoming buy-in challenges
When designing the smart solutions required by VAPL, expert Dr. Seshan commented that, “As with any project that involves change and the introduction of sophisticated technologies, we needed to get buy-in from employees. Fortunately, VAPL employees were willing to cooperate, so implementing the changes was not a problem. Also, the technologies introduced were based on smartphones and tablets, which made it quite easy for them to apply.”
However, a major challenge was bringing the business owners onboard. They understood the long-term advantages of the effort but were concerned initially about the expenditure of time and resources required in the short term. They had to be convinced that the demonstration project would help VAPL become more productive and competitive in the short term. “We had to bring to their attention the reality of losing market share in the not-too-distant future if they did not transform to smart manufacturing. Repeated discussions convinced them that the proposed transformations could be designed to start delivering incremental benefits immediately while creating opportunities for drastic benefits in the longer term,” Dr. Seshan acknowledged.
“Furthermore, we proposed using low-cost IoT devices and innovative processing techniques to keep the investment required as low as possible, showing that the benefits will outweigh the risks,” Dr. Seshan continued. Director Harish emphasized that there was no resistance from VAPL’s workforce to the implementation of the smart technologies. “In fact, our workers enjoyed being trained and picking up these new skills in high technology and management. These include a digital quality management system, IOT devices, and accurate data for decision making by management.”
According to Harish, before the introduction of the smart solutions, VAPL faced problems with: raw material accounting, with shortages to the tune of 2–3% of sales value; product quality, with rejections amounting to 2% of sales value; uncertainty about raw material availability; and lack of visibility. Added Dr. Seshan, “The decisions in the company, from operators to senior management, were not data driven. The metrics collected were prone to error.”
Smart transformation via digitization
Dr. Seshan narrowed the cause of VAPL’s problems to the inability to collaborate in decision making with accurate, real-time information shared among vendors, suppliers, and managers of the material procurement, production, quality, and warehousing functions. Four major issues were therefore addressed in the project action plan:
The demonstration project consultant team was able to resolve the issues by:
The results? Material loss was reduced to essentially zero, while accurate cost-of-quality and overall equipment effectiveness data are now generated automatically. That real-time information is available to material management, production management, and quality management teams simultaneously, allowing them to make informed, collaborative decisions. Current problems in the plant are also reported to the business in real time.
Three simple-to-use smart solutions were therefore successfully adopted by VAPL to achieve the desired results. However, the full achievements of this demonstration company project will only be recognized in about a year to 18 months, when VAPL can document the benefits in the form of increased market share, improved productivity, and reduced costs.
Key benefits of smart solutions
After project completion, a dissemination workshop for about 100 was organized in February 2019 to share the process and outcomes of applying smart technologies and techniques. That workshop demonstrated the viability and benefits of smart technology adoption by MSMEs to a wider audience.
Workshop in Chennai to disseminate the viability and benefits of smart technology adoption by MSMEs, 25 February 2019.
Key benefits to VAPL so far have included improved objectivity, greater real-time visibility of operations, faster responses to exceptions, reduced nonvalue-added activity, vertical integration of plant data with the corporate system, and integration of supply chains. More importantly, the smart solutions introduced ensured that VAPL’s material losses were almost completely eliminated. When adopted by all of its plants, this smart solution alone could save USD32,000 annually.
At the same time, in terms of quality, the 100% visibility of rejects now possible through the digitized process yields objective quality data. The defect characterization feature will be used to identify training needs and process changes, ultimately leading to reduced rejection rates and lowered cost of quality.
VAPL is currently generating objective machine performance data, contributing to more effective decision making, while the material availability tracking system helps the material manager to proactively plan the procurement of raw materials, thus ensuring availability for the next 15 days.
Mapping the road ahead
This APO demonstration company project showed that effective transformation can occur using simple technologies so that the MSMEs can improve profits, competitiveness, and efficiency while reducing costs. What is next for VAPL? Dr. Seshan stated: “Going forward, it must continue to deploy the solutions while planning suitable enhancements. The solutions were implemented in only one plant but must be adopted in all. The next step is to expand ecosystem integration to include all major suppliers and subcontractors.”
Technical expert Dr. Ananth Seshan (L) and NPC India official KVR Raju (C) presenting a certificate of demonstration project completion to Vibgyor Automotive Private Ltd. Director Harish on behalf of the APO.
Director Harish revealed that VAPL had already adopted IT-enabled systems incorporating the fundamentals of smart manufacturing, the IOT, and big data. “Despite this being only a pilot project performed with a batch of 15% of components, the smart technologies introduced during the demonstration project were game changers. We are looking forward to a complete migration to smart manufacturing.”
According to the NPC’s Samdani, the technologies implemented in VAPL were based on “open standards” to address common but significant problems faced by industry. Therefore the changes undertaken could easily be adopted by organizations of similar size in the automotive and other manufacturing subsectors.
“The whole purpose of this project was to motivate industry at large to undertake similar efforts. The cost-effective technology can transform businesses to improve profits, competitiveness, and efficiency, and, most importantly, to reduce costs. Given the success of this project and the relevance of smart manufacturing in the current technology-driven industrial environment, we hope that the APO will support similar projects in other emerging and developing member countries. The NPC India is willing to act as a guide and mentor during such projects,” concluded Samdani.
Photos by NPC India
0 Comments