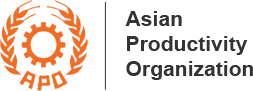
Select Page
Somchay Soulitham shares how learning from an APO session helps her offer better consultancy to SMEs in Lao PDR.
If Somchay Soulitham were the kind of person who thrived on simply staying in her comfort zone, then she never would have applied to participate in an APO project. By her own admission, Enterprise & Development Consultants Company Limited (EDC), the private consulting company she works for in Lao PDR, was not facing any real challenges apart from a disorganized storage and filing system. But as EDC’s founder, Managing Partner, and Human Resources Manager, Somchay could not have only her own interest at heart. People are at the core of her role, and their needs had to be met too, even if they had not yet identified those needs.
“EDC’s job is providing organizational management training for SMEs, private companies, development projects, and government organizations,” she explained. “I saw that APO projects would enrich my knowledge and skills in this area, which I could then transfer to my clients and help them improve too.”
(From left to right) EDC Managing Partners, Consultants, and Trainers Thone Boungvatthana and Somchay Soulitham.
Somchay was accepted as a participant in the APO projects on Training of Trainers in Total Quality Management (TQM) for SMEs held in Indonesia in 2014 and Industrial Engineering (IE) Techniques for Productivity Improvement in SMEs held in Fiji the following year. The APO designed the TQM project in response to challenges faced by SMEs from global competition and sophisticated customers. The project was an immense success among SMEs because it taught how to approach organizations as “systems” and use cost-effective, service-oriented initiatives to fulfill customer needs.
“The different TQM tools provided varied benefits which we are already witnessing in EDC,” Somchay said. “The 5 Sigma (5S) tool, for example, has helped increase the efficiency of our administrative staff. The office is more organized, which means that staff spend less time preparing the materials they need for training courses. Prior to this, they would spend an entire day just putting the stationery together because certain supplies would have run out or gone missing, which meant having to purchase them. The 5S method has helped keep everything organized and accounted for. Another TQM tool that I have found helpful is the fishbone diagram. We’ve introduced it in training courses on continuous improvement.”
The IE project, meanwhile, trained participants in using techniques to analyze and control work processes to boost productivity, reduce costs, and enhance efficiency. Somchay emphasized the importance of work measurement in IE, adding that it helped her be more conscious about working efficiently. “I have now mastered the plan-do-check-act cycle, a management method used for continuous improvement of processes and products. I was also glad to understand ergonomics better. After returning from the training, I decided to invest in new office chairs!”
But mastering and implementing the tools within EDC was only the first step. The next was disseminating this knowledge to her clients. Somchay teamed up with colleague Thone Boungvatthana, also an APO project participant, to design a course called Continuous Improvement for Business Excellence and launched it in March 2015. The course was based on tools from the APO projects the two attended. Divided into four sessions over four days, the course was attended by 84 senior and middle managers and junior staff from four large mining and hydropower companies in Lao PDR.
Somchay reports that the course has been successful with encouraging results ranging from the application of tools to more organized workspaces and better internal processes. “We also run follow-up workshops for participants to review and refresh their learning,” Somchay said. “This is when we hear their success stories.” Sharing more details, she talks about one client who was struggling with a slow procurement process. The company brainstormed to list different causes of the problem, which were then structured into a 5W1H matrix. Next, employees discussed the possible solutions in consultation with EDC and identified adjustments needed. Another client was tackling the late payment of salaries. Managers analyzed the problem and set up new rules like specific dates for submitting information for salary calculations. They later reported that the problem had been solved.
It may be a rosy picture from the outside, but Somchay does not deny that there are challenges behind the scenes. Being in a small company that operates in a small market like Lao PDR, Somchay’s plate is filled with responsibilities, from administrative support services and development programs to organizational development and strategic planning. “I often travel to provinces to conduct training programs,” she pointed out. “This means that I have limited time to spend with my staff in the office. This was why it took two years to implement 5S properly in EDC. But it’s getting better.”
The bigger challenge, however, was that she and Thone had limited practical experience with the tools for TQM and IE. This is where the APO support network proved invaluable. Somchay stays in close contact with friends from the Republic of China, Fiji, Indonesia, IR Iran, the Philippines, and Thailand.
When she shared the progress of her 5S project with them, they immediately jumped in to offer useful inputs based on their own experiences. “In future training courses, I plan to invite them to be resource persons via videoconferencing or Skype. This will enrich our training sessions and the clients will benefit from the opportunity to learn from international practices,” Somchay commented.
Resource persons are the APO’s unique point. Those people, Somchay said, are highly competent with years of experience. She recalled how the resource person assigned to her in her first APO project had dispensed solid advice on using TQM tools and getting the necessary support from management for their adoption. “The other uniqueness of APO projects is the observational site visits, which add so much value as they allow us to learn from real-life practices,” she stated.
Now, Somchay is focused on two main goals. The first is building upon the Continuous Improvement for Business Excellence course. “This year we opened a modified version of the course to the general public. Instead of holding it in four sessions over four days, we split it into two main sessions. The session was organized for three days in June. Participants were then given two months to apply their learning in their workplaces. The second session was in September, when we visited each participant’s organization to assess the actual situation for ourselves. Then we came together to exchange experiences and learning.”
Somchay’s second goal is making 5S a permanent part of EDC’s work culture. To encourage continuous improvement and innovation, EDC management now offers cash incentives to employees whose ideas on making the workplace better are accepted and implemented. Her future initiatives are likely to gain firm support, thanks to the positive results of her training on the company.
“I can confidently say that the APO training contributed to part of EDC’s growth,” she acknowledged. “We have been able to add more topics to our list of training services, which has increased sales by 4%. And we’ve built staff capacity in the areas of 5S, kaizen, TQM, and IE. We can only move forward from here.”
The article was first published in the November–December 2016 issue of the APO News.
0 Comments