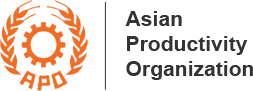
Select Page
Waste does not add any value to a product or service. Toyota engineer Taiichi Ohno came up with seven categories of waste (called muda in Japanese): waiting, transporting, processing, inventory, motion, defects/rework, and overproduction.
Waiting Waiting is encountered everywhere: waiting for a machine that has broken down; delay in arrival of materials; or being late for a meeting. The cause can be bad planning, bad organization, lack of proper training, lack of control, or laziness and lack of discipline.
Transporting Transporting or moving things from one place to another is a common form of waste that does not add value to products. It should be eliminated or reduced as much as possible. There are two aspects to be considered: eliminating the need for transport by better layout; and improving the method of transport.
Processing Processing waste is inherent in design. For example, an electronic typewriter has fewer parts and processes than a mechanical one. Replacing a metal dustbin with a plastic one can reduce several steps in the production process. Using preprinted forms can save paperwork. Unnecessary processing and procedures are other forms of waste.
Inventory When excessive inventory is carried, it ties up valuable financial resources, may deteriorate over time, and takes up space. Work in process and finished stock are also waste.
Motions Movement of equipment or people adds no value. All physical work can be broken down into basic motions. Motion study is one aspect of industrial engineering that assists in reducing wasted motion. Usually this is done by improving the workplace layout, practicing good housekeeping and workplace organization, and introducing low-cost automation.
Defects/rework Waste caused by poor-quality products and defective parts or poor service is a common form of wast. Time must be spent in reworking poor products or addressing customer complaints. Last-minute urgent requirements may disrupt systems and cause delays in delivery to customers. Sometimes poor quality causes accidents.
Overproduction Often manufacturing produces more than is needed. Unused products may have to be discarded when not required later, which is costly. Overproduction is caused by poor planning, poor forecasting, producing too early, and lack of quality control.
Other types of waste identified recently include: untapped human potential; inappropriate systems; and energy and water.
________________________________________
See also: Toyota Production System; Lean Production System