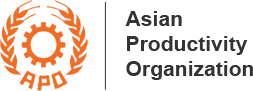
Select Page
The Toyota production system (TPS), sometimes also referred to as the lean production system, refers to the principles and practice of lean manufacturing. The TPS is the systematic elimination of all types of waste. It is also about the implementation of the concepts of continuous flow and customer satisfaction through a flexible production system that allows for flexibility and rapid customization.
The TPS is the philosophy that organizes manufacturing and logistics at Toyota, including the interaction with suppliers and customers. It was largely created by the founder of Toyota, Sakichi Toyoda, his son Kiichiro Toyoda, and the engineer Taiichi Ohno. The focus of the TPS is the elimination of waste and defects at all points of production including input, process, and final output (delivery) through the ingenuity of individual staff and creativity of teams in designing and implementing an error-proof work system. Toyota’s chairman stated: To build [quality] cars we need to build people first. That is in essence the TPS way. Indeed, TPS is also about truly empowering people and giving them the knowledge to be successful. Failures and problems are okay and are viewed as learning opportunities and a way to address the root cause. The true strength of the TPS is the understanding that people are the real strength, not just techniques. Jidoka or ‘autonomation’ with a human touch and just-in-time are two major components of the TPS.” The main goal of the TPS is to eliminate muda, the Japanese term for waste. Seven kinds of waste are targeted in the TPS:
1. Waiting (of operators or machines)
2. Transporting
3. Processing itself
4. Inventory (raw materials)
5. Motion (of operators or machines)
6. Defects(reworking and scrap)
7. Overproduction
Toyota was able to reduce lead time and costs using the TPS while improving quality at the same time. This enabled it to become one of the leading automobile companies in the world. The TPS is a classic example of the kaizen approach to productivity improvement. It is a flexible system to produce various quantities of different products within a very short delivery period. Techniques for the TPS include concurrent engineering, relationships with excellent suppliers, just-in-time production, 5S, total quality management, total productive maintenance, supply chain management, etc. Due to this stellar success of the production philosophy, many of these methods have been copied by other manufacturers. Since the 1980s, the TPS has been so popular that it has been dubbed the least-cost method of manufacturing, or ultimate production system.
________________________________________
See also: 5S or Good housekeeping; 7 wastes; Kaizen; Lean production system