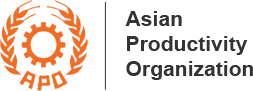
Select Page
Six Sigma was first launched by Motorola in 1987, where it yielded more than 10-fold improvement. Tomkins defined Six Sigma as a program aimed at the near elimination of defects from every product, process, and transaction. Others defined it as a strategic initiative to boost profitability, increase market share, and improve customer satisfaction through the use of statistical tools that can lead to breakthrough quantum gains in quality. Professor Park believed that Six Sigma is a new strategic paradigm of management innovation for company survival in this 21st century, which involves statistical measurement, management strategy, and quality culture.” If deployed correctly, Six Sigma has the ability to generate a host of benefits to businesses, e.g., improving process speed, raising quality levels, reducing costs, increasing revenues, and deepening customer relationships, among others. Six Sigma is implemented in major companies such as GE, AlliedSignal, Dow, DuPont, Ford Motor Company, Merrill Lynch, Toshiba, and the Samsung and LG Group. Six Sigma reportedly enabled billions of dollars in savings as well as sustained earning improvement. Thus Six Sigma is widely regarded as a strategic paradigm for management innovation and business survival. It is used in a variety of industries and business models, from manufacturing to services.